New recruits to Mino Process Control can expect to be integrated into the engineering team from day one. We look to embrace both the skilled and the inexperienced. Training at our office based is mixed with client visits and site experiences. The majority of clients we serve are overseas and hence international travel is an essential part of the job. Working with engineers in their plant locations is always stimulating and challenging. Cultures and practices can be alien but in reality the same goals are sought. Teams are formed, relationships built which form bonds and friendships which last a lifetime. Projects can be merely an upgrade or part of a larger manufacturing plant greenfield site build. Our projects are satisfying and provide piece of mind. You build, install and start large complex machines with state of the art technology. Watch it run, sign off and celebrate another successful project.
Mino Process Control provides not only services to new clients but also to existing. Our engineers support clients through remote connections to existing client installations. Software upgrades can be loaded and transferred, commissioned and run from our office here in the UK. During the pandemic we engaged with our client base and provided remote support in Europe, USA, China and India. Our reach and impact with high speed connectivity and data transfer has revolutionised the way clients receive software upgrades and commission these improvements.
With engineering teams located in China, Europe and North America we can provide a unique local service combined with a full suite of engineering skill sets from our base here in the UK. The combination allows our engineers to work effectively and efficiently without actually leaving the their office station. Whilst practical and on site intervention is always part of the essential service we provide, remote support and servicing is now a firm option for many clients.
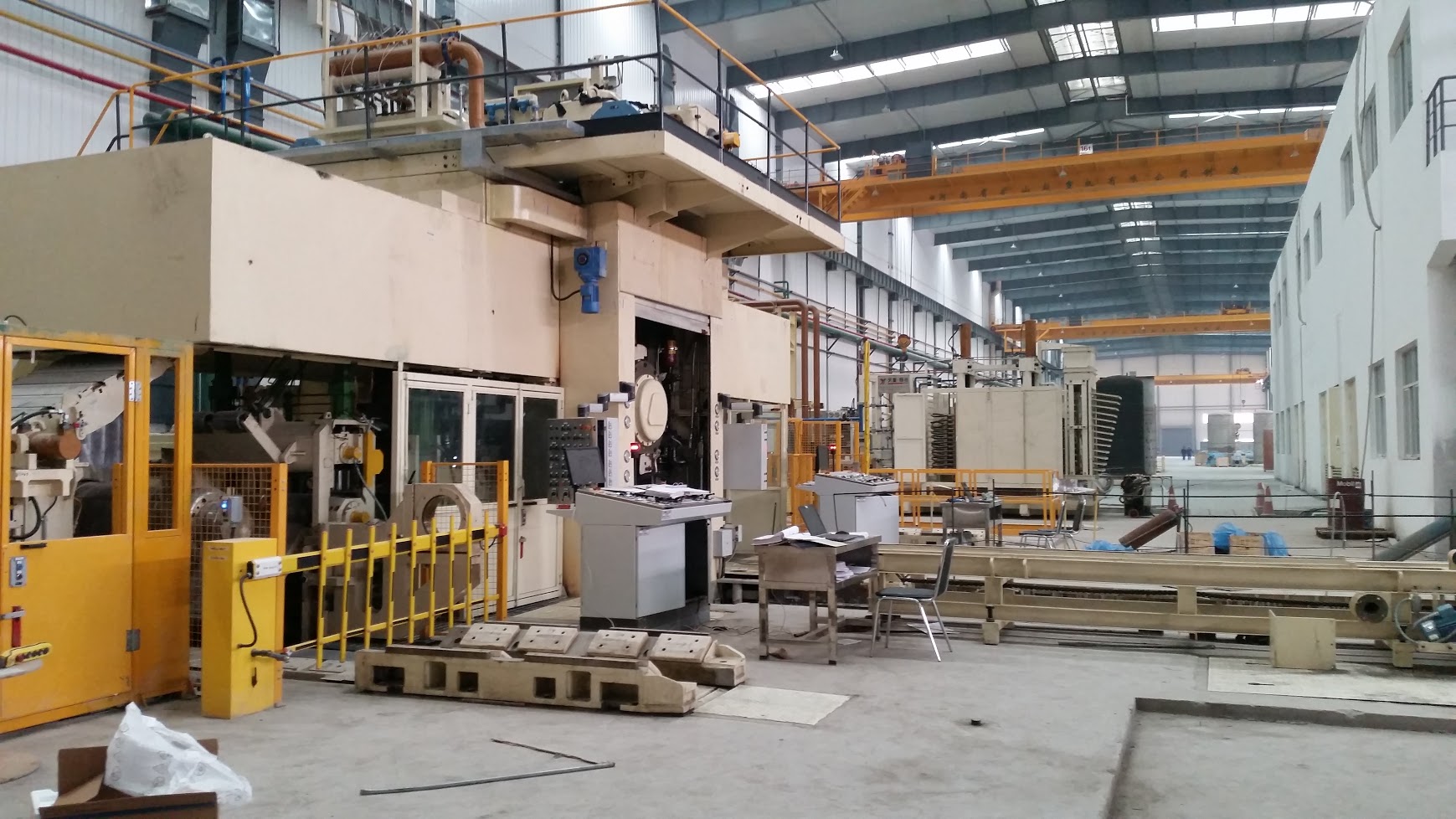